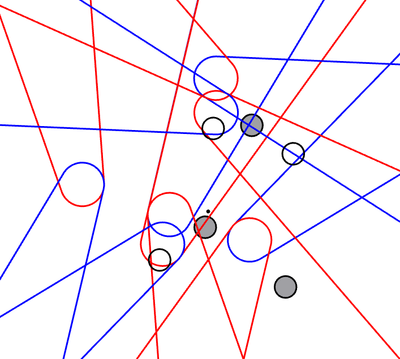
We consider the widely studied problem of reconfiguring a set of physical objects into a desired target configuration, a typical (sub)task in robotics and automation, arising in product assembly, packaging, stocking store shelves, and more. In this paper we address a variant, which we call space-aware reconfiguration, where the goal is to minimize the physical space needed for the reconfiguration, while obeying constraints on the allowable collision-free motions of the objects. Since for given start and target configurations, reconfiguration may be impossible, we translate the entire target configuration rigidly into a location that admits a valid sequence of moves, so that the physical space required by the start and the translated target configurations is minimized.
We investigate two variants of space-aware reconfiguration for the often examined setting of \(n\) unit discs in the plane, depending on whether the discs are distinguishable (labeled) or indistinguishable (unlabeled). For the labeled case, we propose a representation of size \(O(n^4)\) of the space of all feasible translations, and use it to find, in \(O(n^6)\) time, a shortest valid translation, or one that minimizes the enclosing circle or axis-aligned box of both the start and target configurations. For the significantly harder unlabeled case, we show that for almost every direction, there exists a translation that makes the problem feasible. We use this to devise heuristic solutions, where we optimize the translation under stricter notions of feasibility. We present an implementation of such a heuristic, which solves unlabeled instances with hundreds of discs in seconds.